A couple of weeks ago I blogged about aluminium smelting. Today’s topic is a little more prosaic, but historically has been a much more frequent part of building projects.
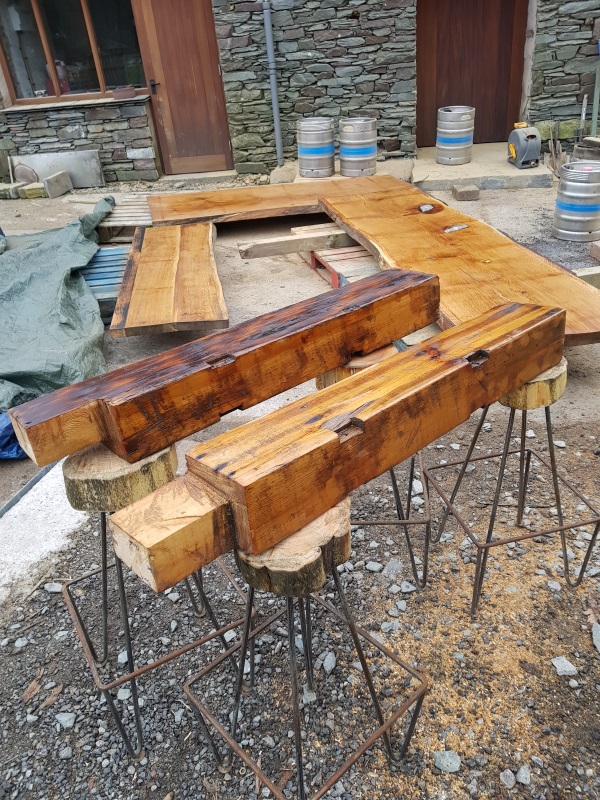
One part of remodelling the bar at The Good Sport is to replace the bar worktop. The old one was a hybrid affair with some chipboard and some stone – the new one is made of wood taken from various sources. There are former house timbers dating from some time in the mid 19th century. They’re very cool, not least for the history they have witnessed. Then there are frame support pieces made just from builders’ merchants supplies, probably pine or something similarly quick growing. But the best sections are two large pieces of oak, rescued by a local craftsman when the tree was felled. These are cut top to bottom along the trunk, so you cannot count the rings and find out how old they are – but my guess is that they considerably outdate the rest of the installation. (The top-to-bottom orientation means that the grain runs along the counter top).
But the thing I want to talk about today is not the age of the wood, but the preparation that has gone into it. The two pieces had been supplied to us reasonably smooth – but “reasonably smooth” menas “not smooth enough” when it’s a thing that people will be leaning on. So one of my jobs these last few days has been to turn “reasonably smooth” into “really smooth”.
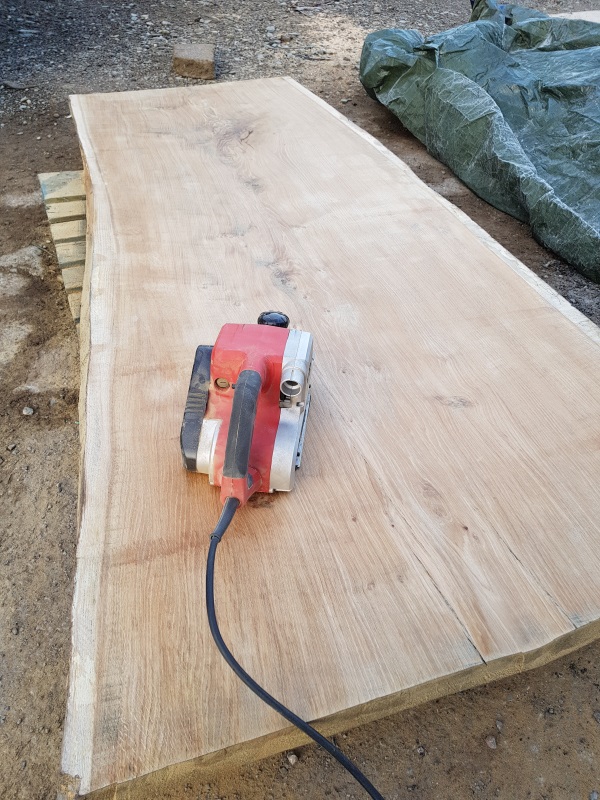
Now, since this is 2019, I used a selection of power tools to effect this change, mostly a belt sander with a number of different grades of sandpaper. Even with that, it took a decent time to go over the top surface multiple times, working from coarser to finer passes. I was extremely happy with the result, but it also led me to consider how things might have been in the many ages of our world before power tools were invented. After all, sanding wood is an activity which lends itself to thinking about other things while you’re working away. How long, I mused, would this have taken me if I was doing it all by hand? And would the final result have been anything like so pleasing? After all, wood-smoothing is not something that I have done much of in my life to date, and I wouldn’t call myself especially skilled at it.
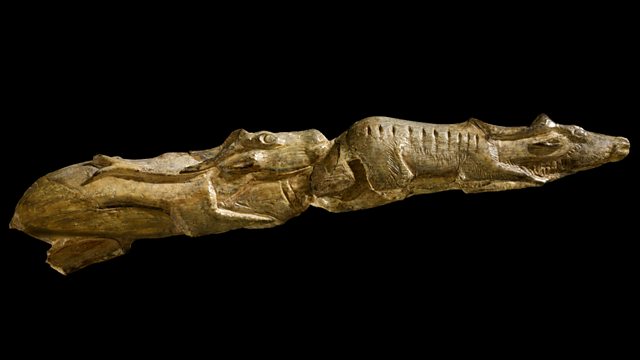
Human history is full of exquisitely crafted objects, meeting needs somewhere between religion, art, and practical necessity. This swimming reindeer figure was made around 13,000 years ago – I don’t know how long it took the original artist to fashion it, but I’m guessing that it was rather longer than the time I put into smoothing two essentially flat pieces of wood. Not to mention the huge number of practice hours he or she had put in since childhood.
Now, I only smoothed one side of the wood – the pragmatic nature of today’s world means that I wasn’t motivated to do much to the hidden side except to make sure it was proof against various kinds of wood pests. But back in the day, if the kings or the priests felt it important to take just as much care on the hidden side as the visible one, then you would just have got on with it.
Which brings me to the future. There’s a developmental principle in some games – those in which the time frame of the game is spread out over many years – that items which are available only to the wealthy in one era get diffused more and more widely through the population as a whole as you go forward in time. I guess the standard example is computing power – back in the 1950s and 60s, computers could only be owned by large institutions or extremely wealthy individuals. Now we all have much more powerful machines we carry around in our pockets. Similarly for smooth bits of wood – once upon a time it took real skill and craft to create something smooth and shapely from a rough-hewn piece of timber. Nowadays anyone who wants can go out and buy power tools and achieve something similar by themselves (not necessarily with artistic flair, but certainly with polish).
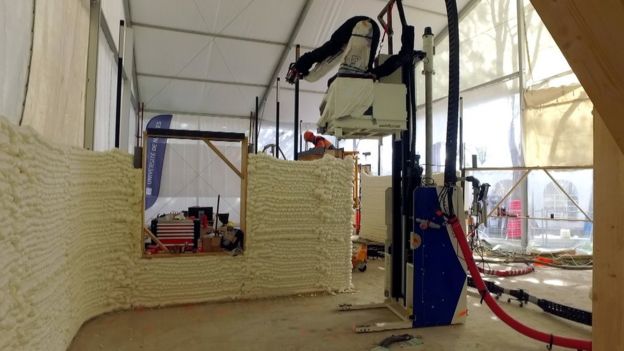
Now, as and when we get to build colonies and habitats in various places around the solar system, my bet is that we will use 3d printing as our construction technique. After all, it’s way simpler and cheaper to ship out a large printer to wherever you’re going, and use that to construct tools, equipment, and habitat sections – much cheaper than paying for the fuel to send actual construction materials. That’s very cool, but unless the technology advances in aesthetic ways as well as practical ones, I can’t see 3d-printed building materials having a wood grain that can be sanded and then picked out with oil. On one level it doesn’t really matter – you’d prefer that your house on, say, the asteroid Ceres was airtight and warm, even if that meant not having a wood grain to look at. Or maybe we’ll have a printer add-on that will simulate the grain in whatever direction you want.
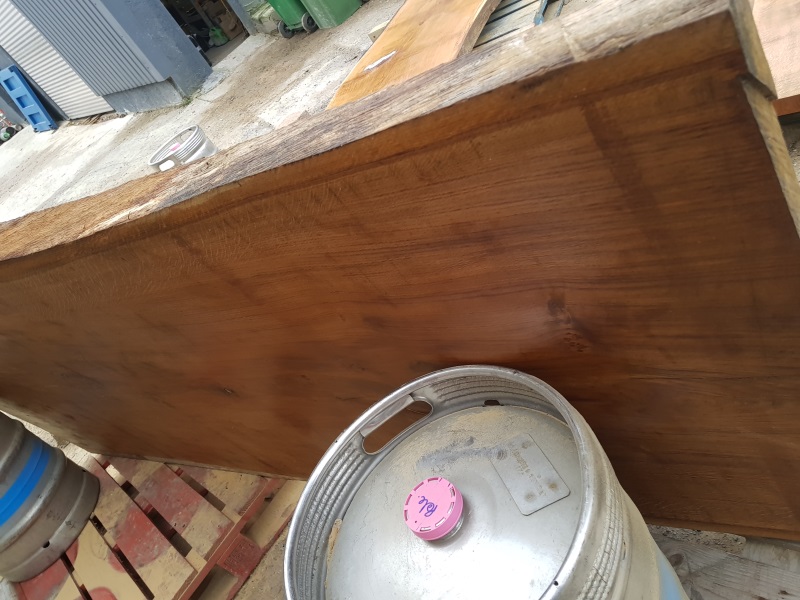